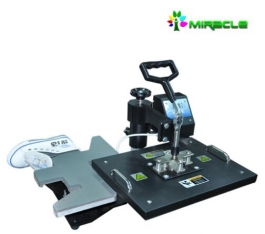
An Analysis on factors affecting heat press quality
An Analysis on factors affecting heat press quality
Description
The reasons to affect heat press quality are as follow: pressure, temperature, the quality of heat transfer inks and other factors.
1. Pressure
Pressure is an important factor in heat press technology. Take the sublimation transfer printing fabric as an example. If the pressure is too low and the gap between fabric and transfer paper is too big, which will cause low quality of the finished products. If the pressure during printing process is too large, deformation and morphological changes will occur, which will cause the shortcomings of crude toughing and colored surface. As long as we can adjust proper pressure, and the gap between fabric and transfer paper, good quality fabric can be made.
2. Temperature and time
The temperature and time required is about 180℃~230℃, 10-30s during printing process.
3. Heat transfer inks
Heat transfer inks consists of dyes, connecting material, solvent and additive. Dyes have the charateristics of the ability of sublimation transfer and permeability. The connective materials have small connection with dyes, which result in easily releasing dyes and proper printability, preservation and thermal transfer adaptability. The most common used connective materials are ethyl cellulose, EHEC and Long oil modified alkyd resin. The solvents usually used are turpentine, terpineol, high boiling aromatic alcohols, alkanes and cellosolve.
4. Others
Apart from temperature, time and heat transfer inks, something during printing process also will have effect on the quality of finished products, including heat transfer paper, the differences of color before printing and after printing, compact paste between heating plate, heat transfer paper and transferred materials.
1. Pressure
Pressure is an important factor in heat press technology. Take the sublimation transfer printing fabric as an example. If the pressure is too low and the gap between fabric and transfer paper is too big, which will cause low quality of the finished products. If the pressure during printing process is too large, deformation and morphological changes will occur, which will cause the shortcomings of crude toughing and colored surface. As long as we can adjust proper pressure, and the gap between fabric and transfer paper, good quality fabric can be made.
2. Temperature and time
The temperature and time required is about 180℃~230℃, 10-30s during printing process.
3. Heat transfer inks
Heat transfer inks consists of dyes, connecting material, solvent and additive. Dyes have the charateristics of the ability of sublimation transfer and permeability. The connective materials have small connection with dyes, which result in easily releasing dyes and proper printability, preservation and thermal transfer adaptability. The most common used connective materials are ethyl cellulose, EHEC and Long oil modified alkyd resin. The solvents usually used are turpentine, terpineol, high boiling aromatic alcohols, alkanes and cellosolve.
4. Others
Apart from temperature, time and heat transfer inks, something during printing process also will have effect on the quality of finished products, including heat transfer paper, the differences of color before printing and after printing, compact paste between heating plate, heat transfer paper and transferred materials.